MRP Mobile Inventory Management Software
FEATURES AND BENEFITS
Redthorn’s new Mobile Inventory Management Module allows customers to utilise touch screen tablets to control all areas of material and manufactured product handling and management on the shop floor. It does this by expanding on the current Barcoding system to utilise mobile tablet technology.The new module’s functionality ranges from receipting delivered materials at goods inwards into stock through to manufactured jobs being allocated into stock ready for despatch.
Mobile Inventory Management Module
FEATURES AND BENEFITS
Redthorn’s new Mobile Inventory Management Module allows customers to utilise touch screen tablets to control all areas of material and manufactured product handling and management on the shop floor. It does this by expanding on the current Barcoding system to utilise mobile tablet technology.The new module’s functionality ranges from receipting delivered materials at goods inwards into stock through to manufactured jobs being allocated into stock ready for despatch.
BENEFITS:
- Increased operational efficiency through standardization of operations
- Reduction in occurrence of errors in work
- Reduction in time wasted on movement of staff during non-value-added operations
- Management of WIP on the shop floor
- Revealing loopholes in production or processesIncreased productivity of staff
- Positive impact on the revenue of a manufacturing business
FEATURES:
- Allows the booking of delivered materials goods directly into stock
- Amendment of stock quantities at the physical stock location
- Alteration of stock location at the physical stock site
- Allows the booking of material back from sub contract directly into stock
- Allocation of materials and sub-assembly stock to manufacturing jobs
- Reduction or removal of materials and sub-assembly stock from manufacturing jobs
- Allows the booking of finished goods directly into stock and marking the manufacturing job complete
- Includes ability to add a new schedule lines to manufacturing jobs
- Amendment of finished goods stock quantity at the physical stock location
- Alteration of finished goods stock location at the physical stock location
Stay in touch with your inventory. Manage your inventory from the palm of your hand.
Stay in touch with your inventory. Manage your inventory from the palm of your hand.

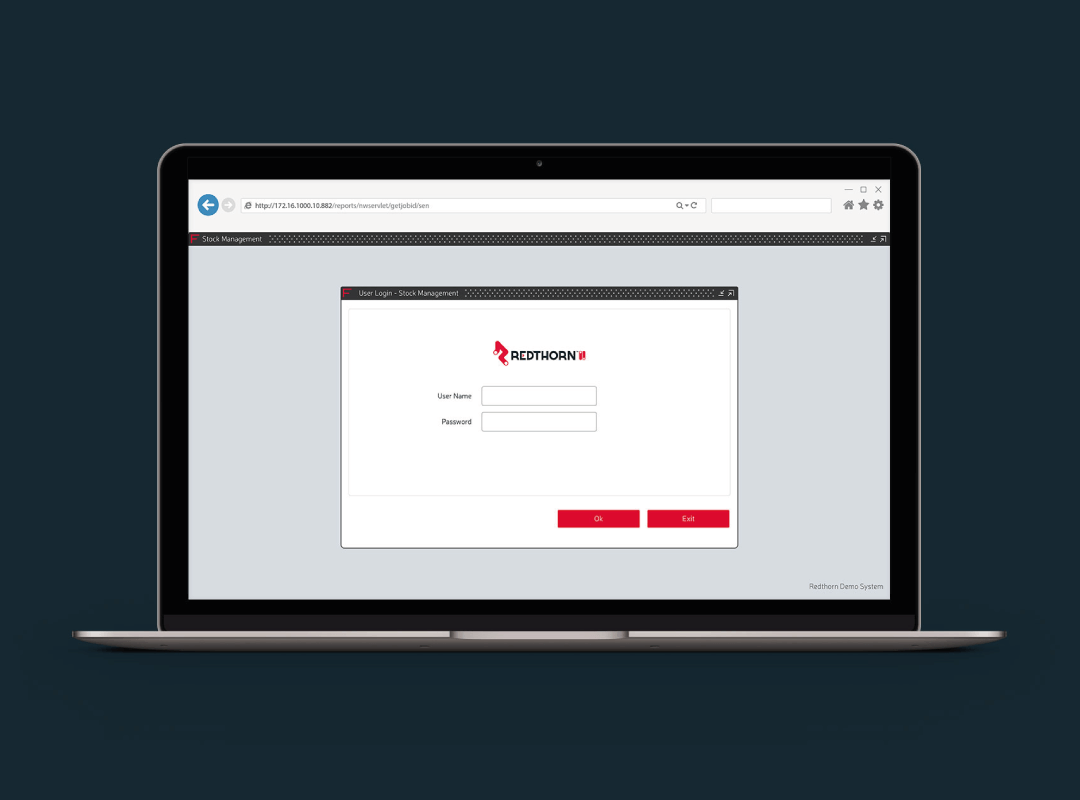
User Manual
The application launches using the tablet shortcut (like a Redthorn Touchscreen)
Log in as a user would in the system
Note – the development uses a touch screen licence)
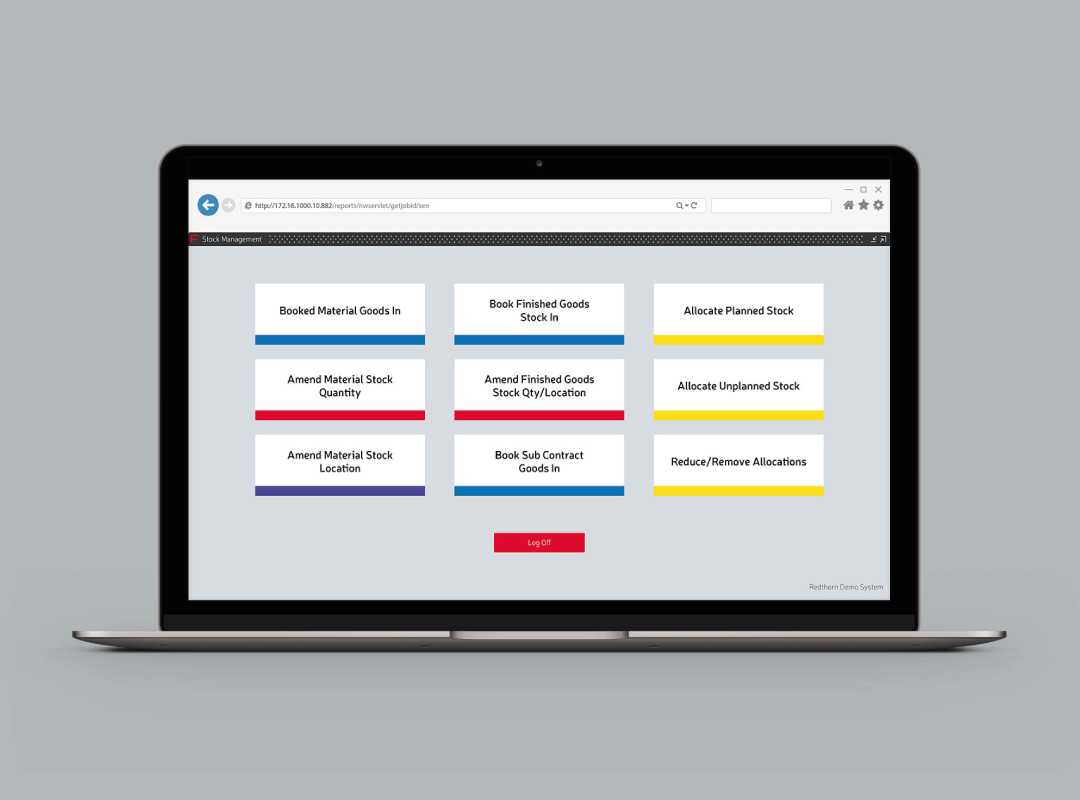
User Manual
Once logged in main screen looks as below.
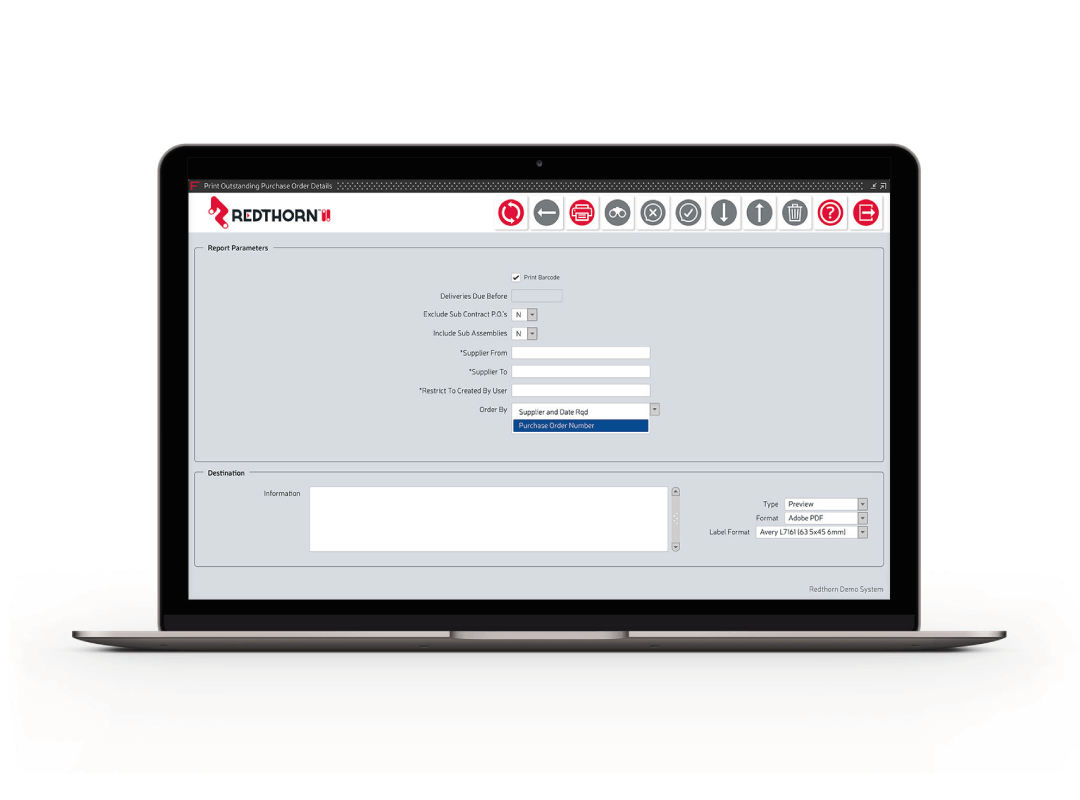
Booking of delivered Materials Goods Directly Into Stock.
Open Home Page – click ‘Book Material Goods In’
Prior to using tablet you can print ‘Outstanding Purchase Order Details’ report in the system. This report is for use with ‘Book Material Goods In’ button and ‘Book Sub Contract Goods In’ button.
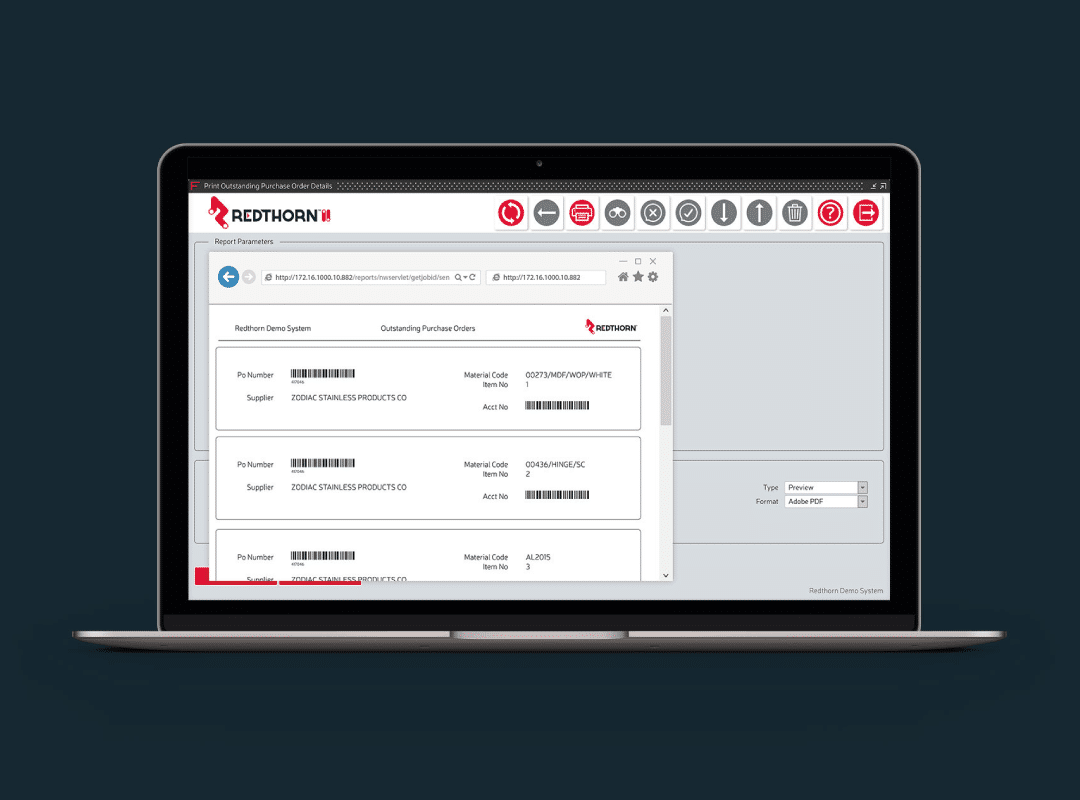
Booking of delivered Materials Goods Directly Into Stock.
A ‘Print Barcode’ function has also been added to ‘Print Outstanding Orders Report’, also both order by’s now available, in case you are booking in via supplier or PO number.

Booking Material Goods In
Open Home Page – Amend Material Stock Quantity
Scan the gin no or location from the gin labels above. This gives the ability to change the in stock quantity.
When you save the ‘Print Barcoded Stores Label’ is produced as described above.
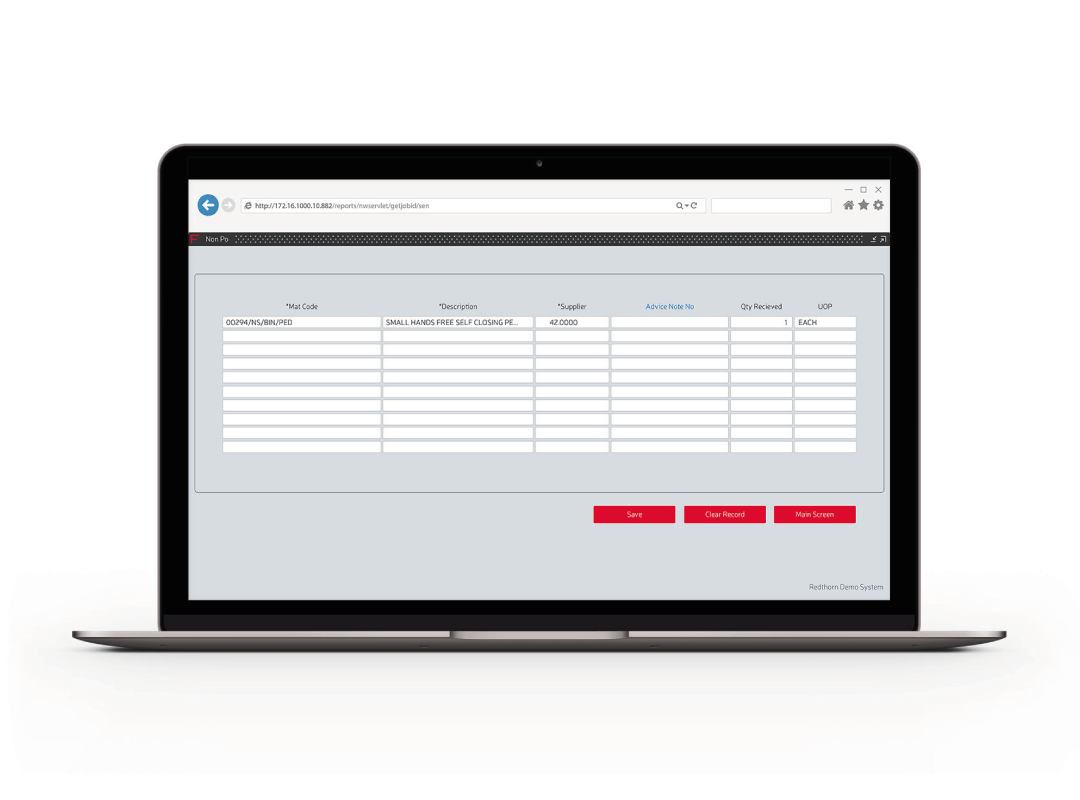
Booking Material Goods In
Note – there is the option if booking in via no po number (i.e. 99 in) from button on screen above. When you save this form, the ‘Print Barcoded Stores Label’ is produced.
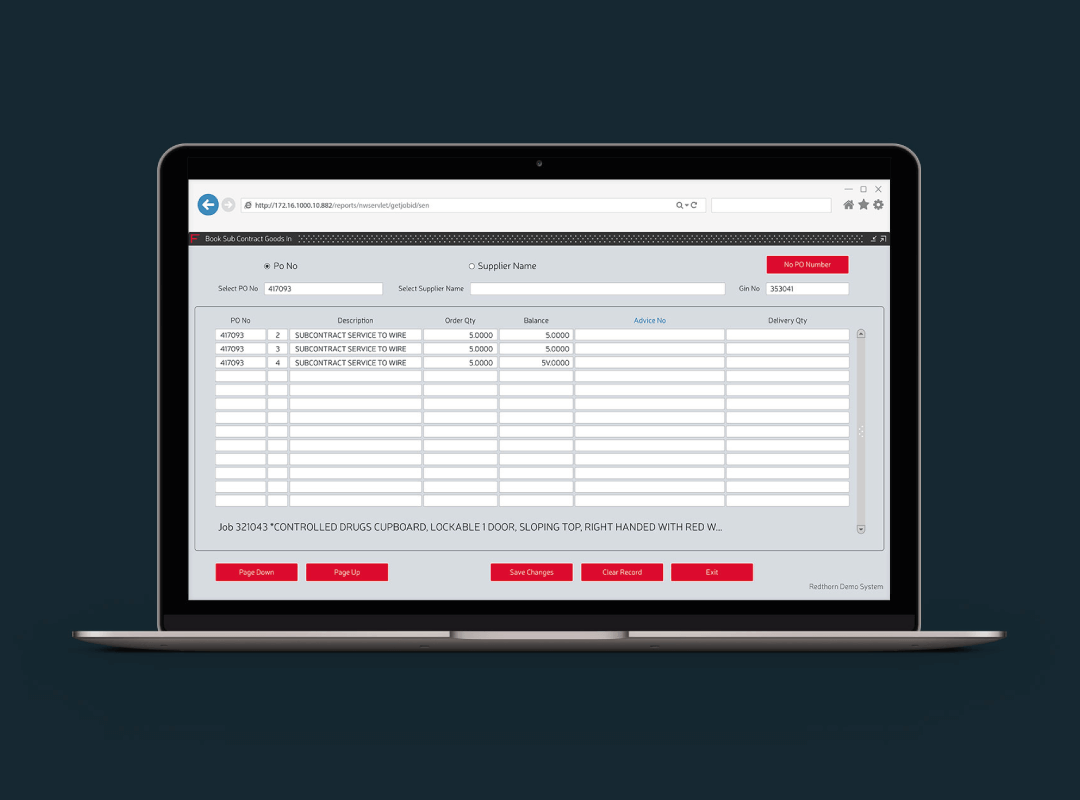
Book Sub Contract Goods In
Open Home Page – click ‘Book Sub Con Goods In’
The system offers the facility to scan via PO number or via supplier name, from the outstanding purchase orders report above.
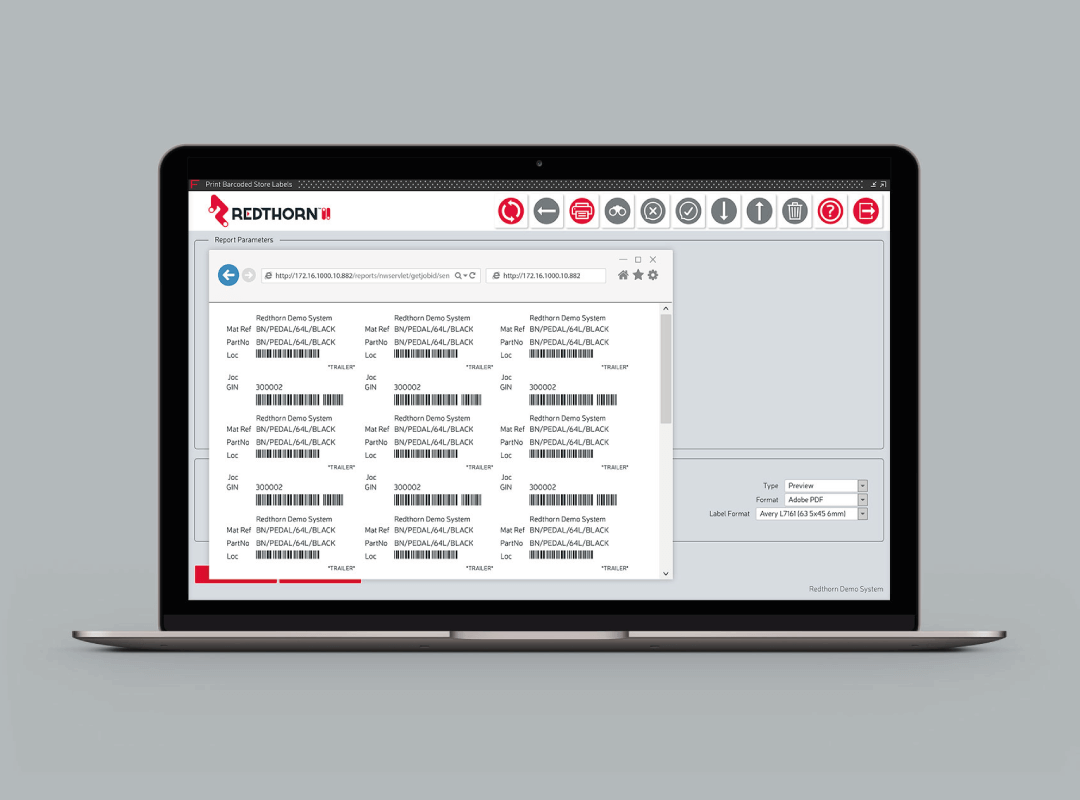
Book Sub Contract Goods In
When you save the ‘Print Barcoded Finished Goods Location Labels’ an Avery sized label is produced (more info below).
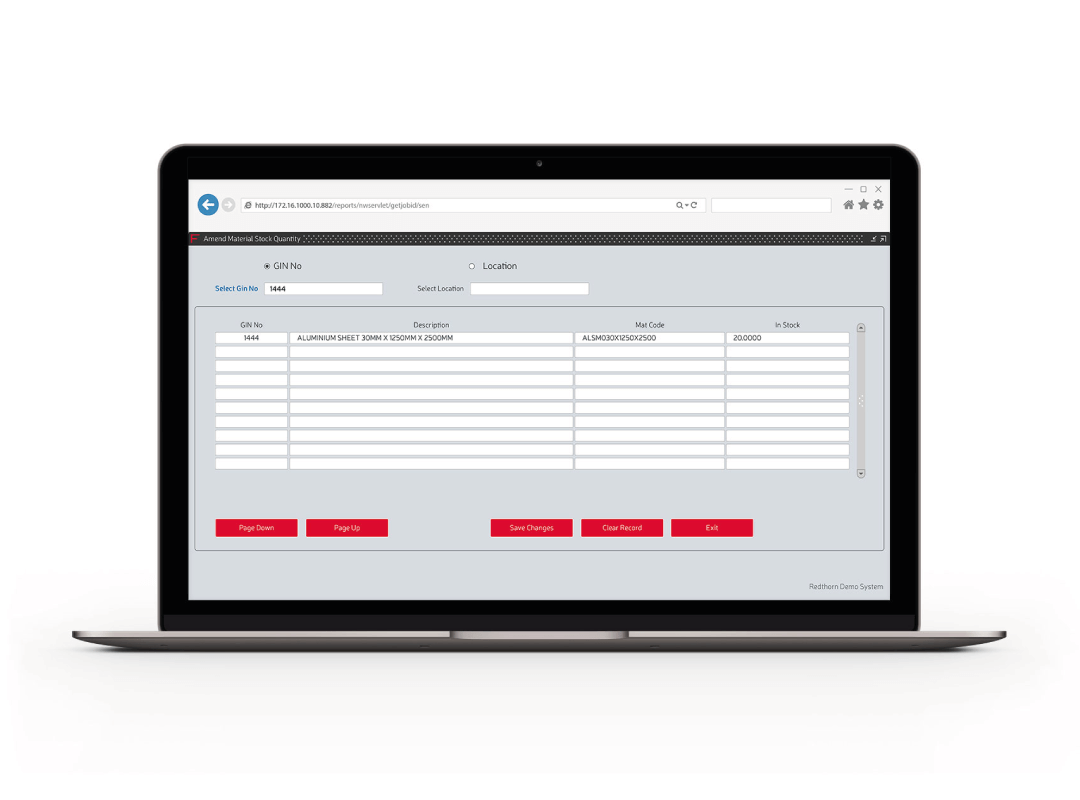
Amend Material Stock Quantity
Open Home Page – click ‘Amend Material Stock Quantity’
Scan the GIN No. or location from the gin labels above. This gives the ability to change the in stock quantity
When you save, the ‘Print Barcoded Stores Label’ is produced
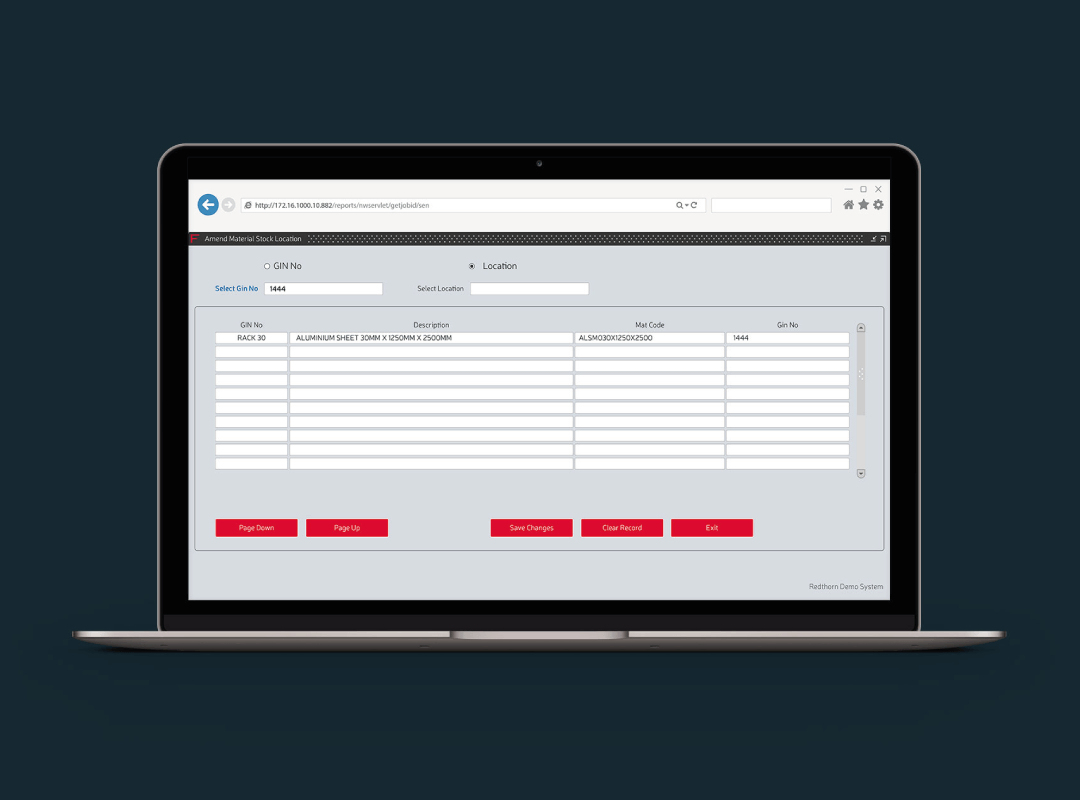
Amend Material Stock Location
Open Home Page – click ‘Amend Material Stock Location’
Scan the GIN No. or location from the GIN labels
Change the location by either typing or scanning a location
When you click save, the ‘Print Barcoded Stores Label’ is produced
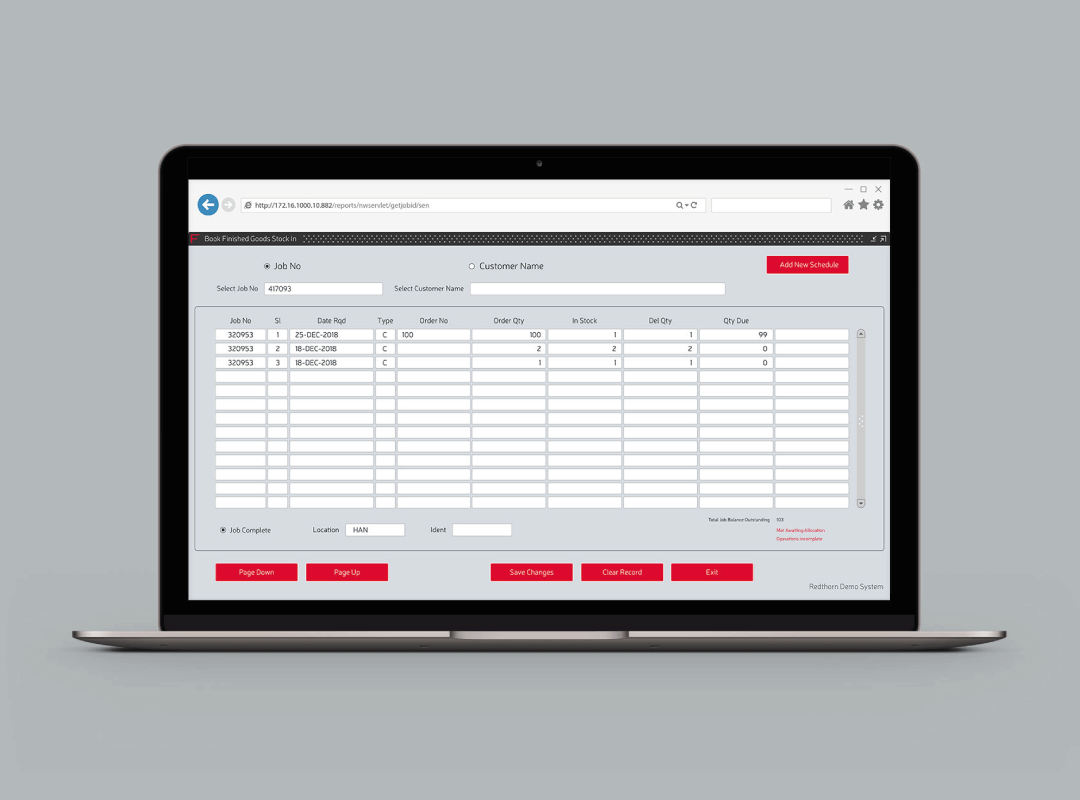
Book Finished Goods Stock In
Open Home Page – click ‘Book Finished Goods Stock In’
Scan job card or select customer (which will show all live jobs for that customer)
Enter quantity (required), location (can scan) and ident (if a sub assembly)
Mark job complete at this stage if required
The module also offers the ability to add a new schedule like you can via ‘Create a Delivery’ screen
When you click save, the ‘Print Barcoded Finished Goods Location Labels’ an Avery-sized label is produced
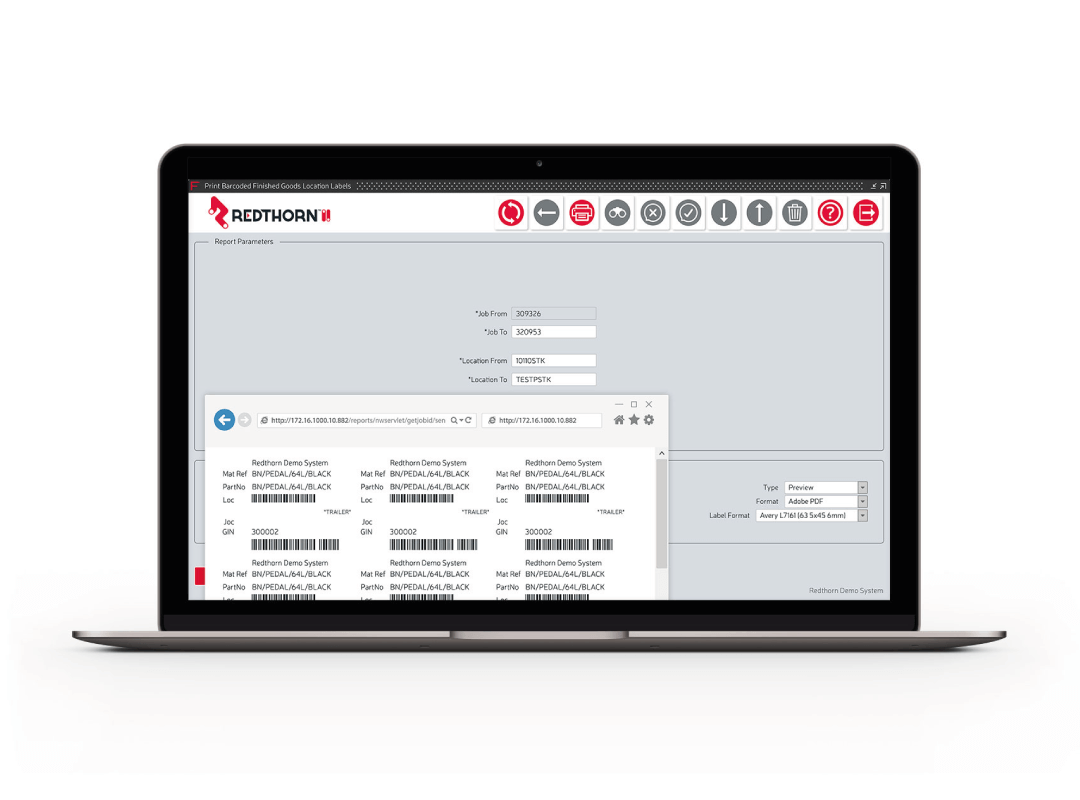
Book Finished Goods Stock In
New label created, called ‘Print Barcoded Finished Goods Location Labels’. Has the job number and location as barcode, to be used with ‘Amend Finished Goods stock’ button on tablet:
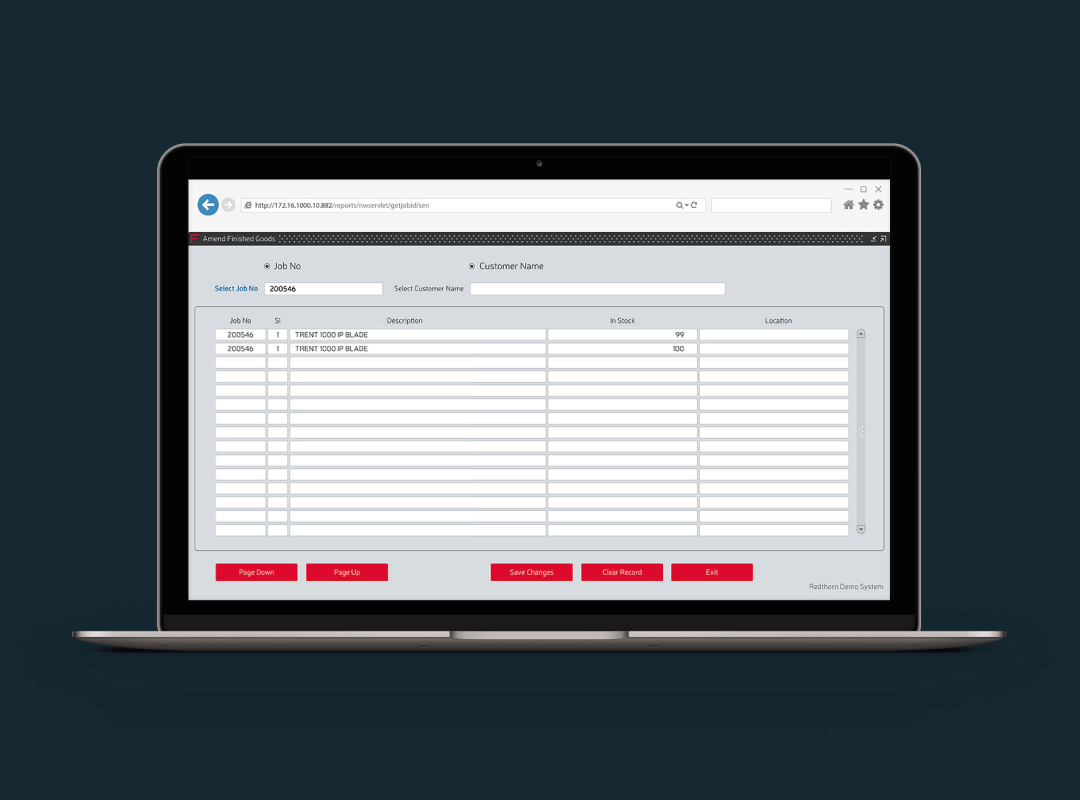
Amendment of Finished Goods Stock Quantity at the Physical Stock Location
Open Home Page – click ‘Amend Finished Stock Location’
User can scan the job number or the location and then amend the location or the stock quantity
When you click save, the ‘Print Barcoded Finished Goods Location Labels’ is produced
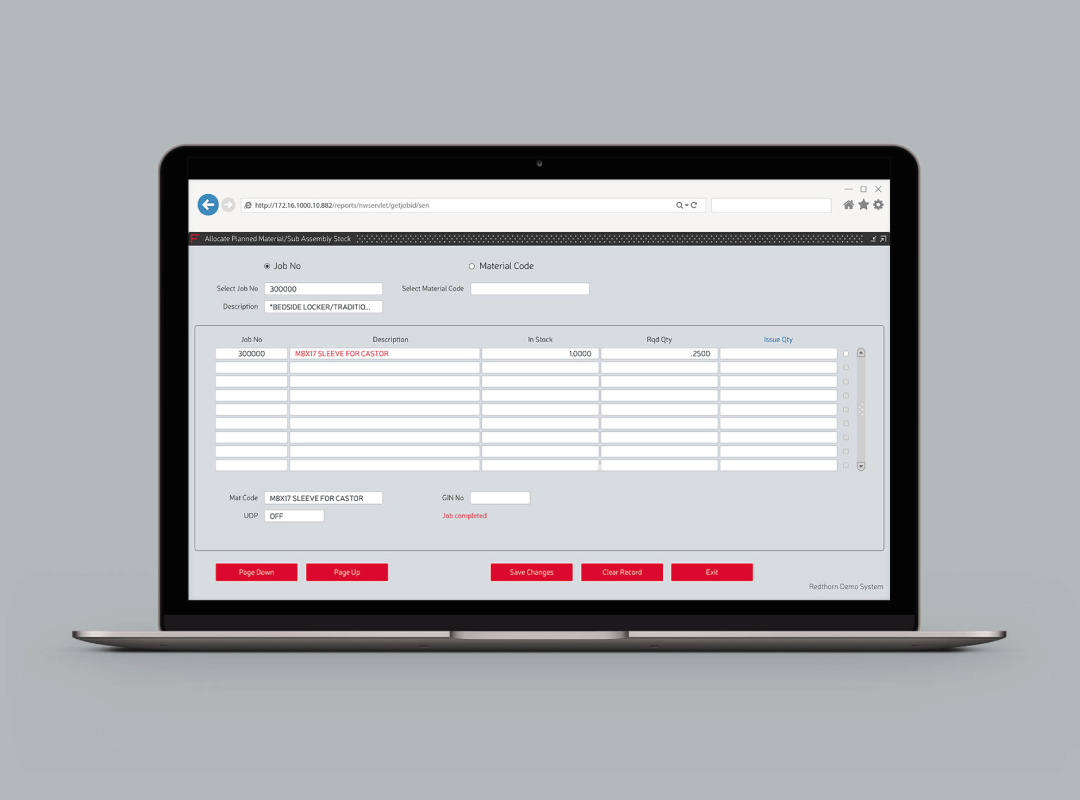
Allocate Planned Stock
Open Home Page – click ‘Allocate Planned Stock Button’
Scan a job number from a job card or a select a material code. Note – user can also scan a material code via crystal
Enter the allocated quantity and tick the box. Note – to enter the full quantity to allocate, ticking the box will enter the full issue quantity.
If a specific GIN No. is required, select the GIN No. from the box at bottom of the screen. User can also scan the GIN No. from the GIN label.
Issue quantity is via UOM. If you want to issue via UOP, double click in ‘Issue Qty’ to get UOP box
Red job description points you to a message at the bottom of the screen saying ‘job completed’
If allocating sub assembly jobs, the GIN No. LOV will show on the MFR job number
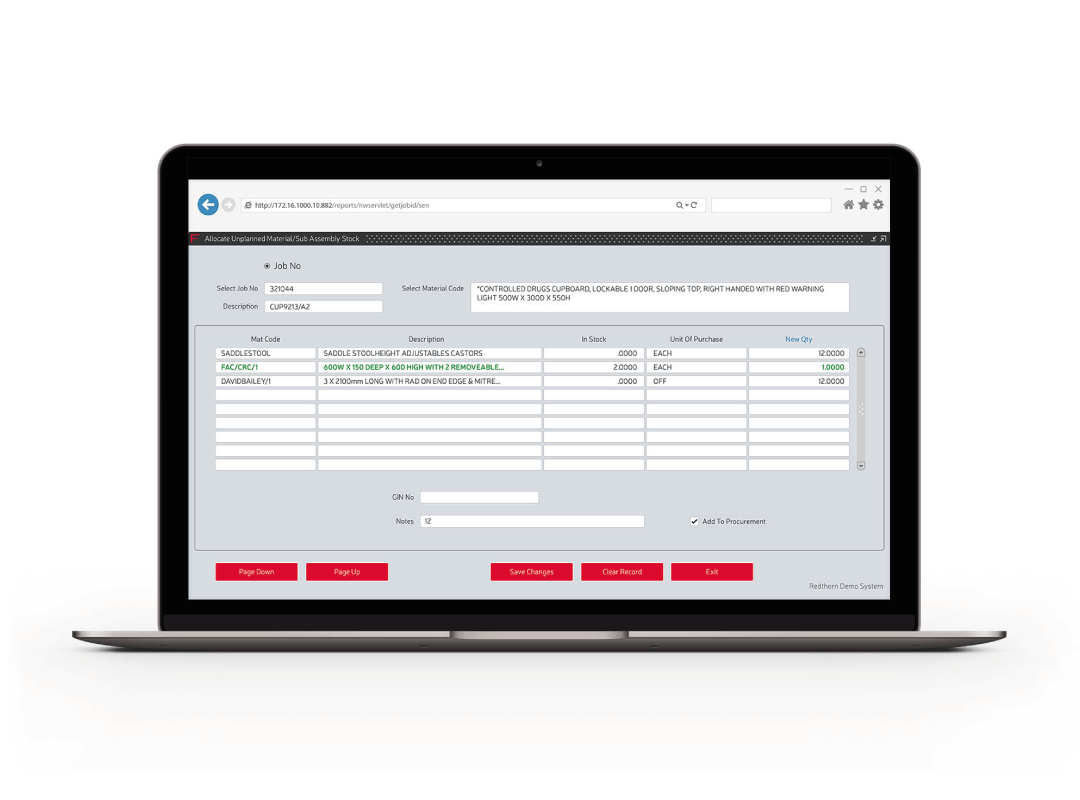
Allocate Unplanned Stock
Open Home Page – click ‘Allocate Unplanned Stock’
Scan the job number, the screen will be blank for you to select the mat code. Enter a quantity and click ‘save’. Note – this can also be used to select a specific GIN
Green in example below is due to ticking the ‘Add to Procurement’ flag as there was no stock
If the user forgets to check this box and system has none in stock it will add to procurement anyway
Issue quantity is via UOM. If you want to issue via UOP, double click in ‘Issue Qty’ to get UOP box
Note – user can also add their own notes
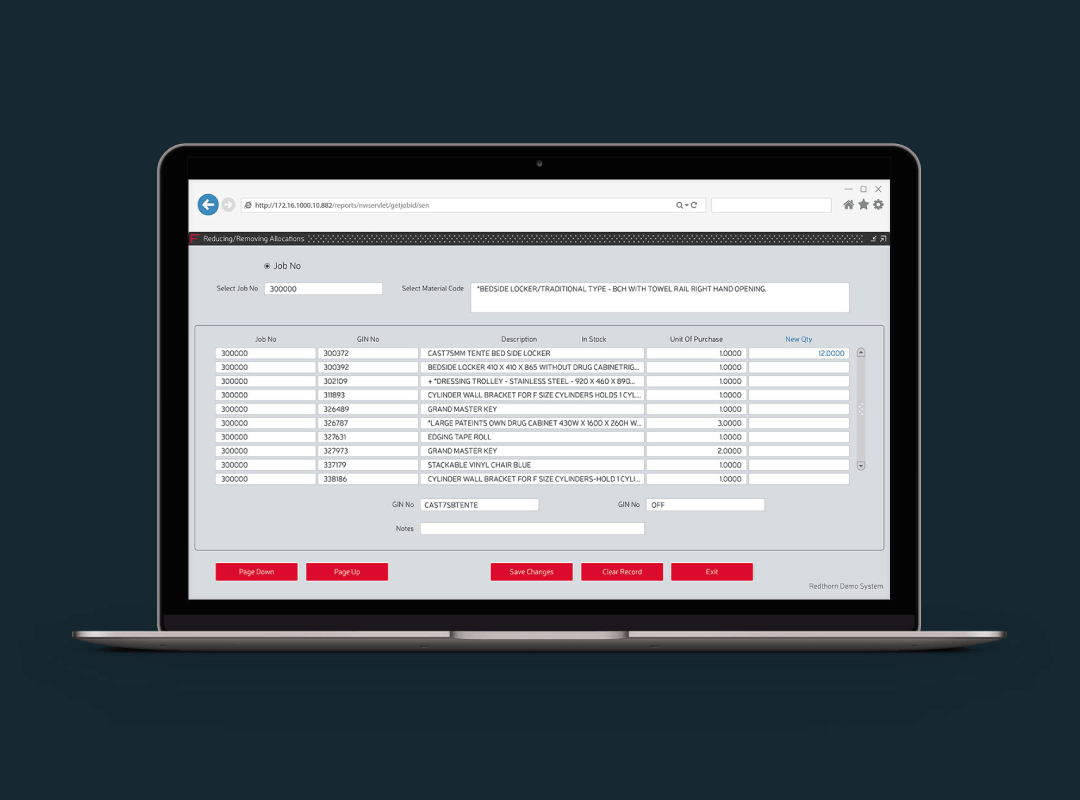
Reduce/Remove Allocations
Reduce/Remove Allocations
Open Home Page – Click Reduce Remove Allocations
Scan job number. Like the system screen, enter a new qty. Entering a qty of 0 will remove the allocations completely.
As above qty is via UOM if you want to issue via UOP double click in Qty to get UOP box.
Note that the user can add notes
NEED MORE INFORMATION?
Download our factsheet now
NEED MORE INFORMATION?
Download our factsheet now
REQUEST A DEMO
Don’t just take our word for it.
Our software supports over 600 engineering and manufacturing businesses worldwide. Enter your email to request a product demonstration.
REQUEST A DEMO
Don’t just take our word for it.
Our software supports over 600 engineering and manufacturing businesses worldwide. Visit the Knowledge Centre for more information or contact us to talk about how we can help your business grow.
Error: Contact form not found.
CONTACT US
Redthorn (UK)
28 Momentum Place
Bamber Bridge
Preston
PR5 6EF
+44(0) 1772 336 944
Redthorn (Australia)
Suite 5, Level 1
190 Queen Street
Melbourne VIC 3000
SNC Solutions (Sales & Support)
1300 356 976